Corning
Optical Fiber, Abatement Plants |
William
Blythe, Stannic Chloride Plant |
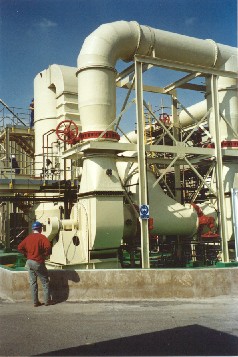 |
These
three TURBOSCRUBBER® units were installed over a 2 year period with
last unit commissioned in the summer of 1999. They are installed on
the backend of existing abatement plant (bag houses and low pressure
Venturi scrubbers) to perform a polishing role to substantially reduce
emissions. The units simultaneously scrub fine silicone dioxide particles
and absorb Cl2 and HCl gases to maintain emission levels below the
enhanced legislative requirements now required. The unique non-clogging
feature of the TURBOSCRUBBER® ensures reliable and consistent operation
without any increase in gas side pressure drop. |
|
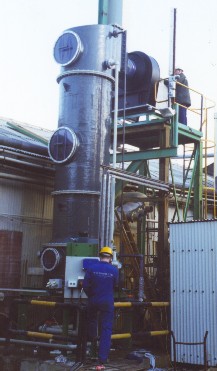 |
Installed in 1998 this Turboscrubber® unit treats the exhaust gases
from various reactors, stills and packaging stations in the Tin Plant
Recovery Section. The unit simultaneously scrubs SnCl4 vapours, their
hydrolysis product HCl, and SnO2 precipitate to high efficiencies.
It was supplied as a replacement and upgrade for an existing packed
column scrubber which was prone to blockage by the precipitated solids.
The SnO2 precipitate is discharged with the spent scrubbing liquor
and its valuable tin content recovered. |
|
|
|
Borden
Chemicals, Formaldehyde Plant |
Engelhard,
Metals Recovery Incinerator |
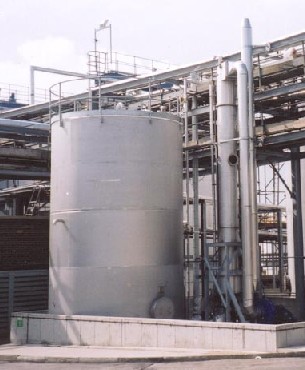 |
This TURBOSCRUBBER®
plant, which was commissioned in the winter of 1999, is designed to
treat the vapours venting from several storage tanks, reactors and
other process plant, both under normal operation and during peak conditions
when transfer, filling and emptying operations are being carried out.
The scrubbing liquid (water), having absorbed the gases, is handled
within the existing site process and treatment systems. The high mass
transfer rates uniquely generated by the TURBOSCRUBBER® system are
able to give the very high removal efficiencies required for such
a compact plant. |
|
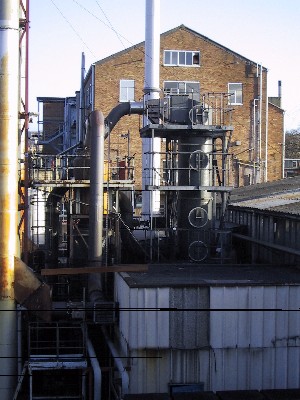 |
Engelhard’s
metal recovery incineration plant was upgraded in 1997 and 1998 to
improve combustion and pollution control. A TURBOSCRUBBER® system
was installed in series with an existing venturi scrubber to reduce
high fine particulate loadings up to 750 mg/m3 down below 10 mg/m3,
absorb HCl, and to cool gases for efficient plume suppression. Additionally
a sophisticated control system was designed and installed for flexible
operation of this versatile plant. |
|