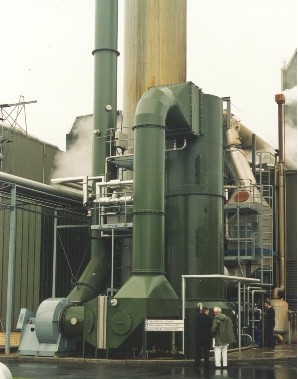 |
Commissioned in the winter of 1997
this TURBOSCRUBBER® unit simultaneously scrubs fine soot particles
(product of HSFO fuel boilers), absorbs SO2 gas, and recovers waste
heat. The scrubbing medium is process effluent which typically has
pH 8 to 12. This effluent was originally neutralised with acid (HCl)
before discharging via a biological treatment plant. The operation
of the TURBOSCRUBBER® is set such that the SO2 removal from the
boiler flue gases is controlled to match that required to both neutralise
the process effluent (without further chemical treatment) |